How to Calculate Service Level in Inventory Management? Everything you need to know
Inventory management is the Inventory management is the backbone of any business that deals with physical goods. One of the most critical metrics in this domain is the “service level,” which measures how well your inventory meets customer demand. Achieving the right service level can significantly impact your business’s efficiency, customer satisfaction, and profitability. In this article, we’ll explore how to calculate the service level in inventory management, its impact on operations, and how to optimize it for your business.of any business that deals with physical goods. One of the most critical metrics in this domain is the “service level,” which measures how well your inventory meets customer demand. Achieving the right service level can significantly impact your business’s efficiency, customer satisfaction, and profitability. In this article, we’ll explore how to calculate the service level in inventory management, its impact on operations, and how to optimize it for your business
What is Service Level in Inventory Management?
Service level in inventory management refers to the probability that your inventory will meet customer demand without stockouts. It’s typically expressed as a percentage and is crucial for maintaining customer satisfaction and ensuring smooth operations. A higher service level means you are more likely to meet customer demands, but it also usually requires holding more inventory, which can increase costs.
Service Level and Its Impact on Inventory Management
Service level plays a pivotal role in balancing customer satisfaction with inventory costs. A low service level might lead to stockouts, lost sales, and unhappy customers, while a very high service level could mean overstocking and increased holding costs. Therefore, determining the optimal service level is essential for effective inventory management.
CheaperTeam is a European based outsourcing company with headquarters centrally located in the heart of Manhattan, NY. Our objective is to provide high-quality, motivated employees while maintaining cost efficiency for businesses. We offer a boutique style of doing business, allowing flexibility in vetting and sourcing employees for various industries. Our staff comprises data entry specialists, medical billers, interior designers, back-office employees, and virtually any position that can be executed remotely.
What Does a 97% Service Level Mean?
A 97% service level means that there is a 97% probability that you will have enough inventory on hand to meet customer demand without facing a stockout. In practical terms, this means that out of every 100 customer orders, only three might not be fulfilled due to a lack of stock.
Optimal Service Level Formula (Supply Chain)
How to Calculate Service Level in Inventory Management
Calculating the optimal service level involves a few key factors, including the cost of stockouts and the cost of holding inventory. Here’s a basic formula to calculate service level:Service Level=Cost of StockoutCost of Stockout+Cost of Holding Inventory\text{Service Level} = \frac{\text{Cost of Stockout}}{\text{Cost of Stockout} + \text{Cost of Holding Inventory}}Service Level=Cost of Stockout+Cost of Holding InventoryCost of Stockout
Cost of Stockout refers to the potential revenue loss, customer dissatisfaction, and any additional costs incurred due to a lack of inventory.
Cost of Holding Inventory includes warehousing costs, insurance, depreciation, and the opportunity cost of capital tied up in inventory.
The goal is to find a balance where the service level is high enough to avoid stockouts but not so high that inventory holding costs become prohibitive.
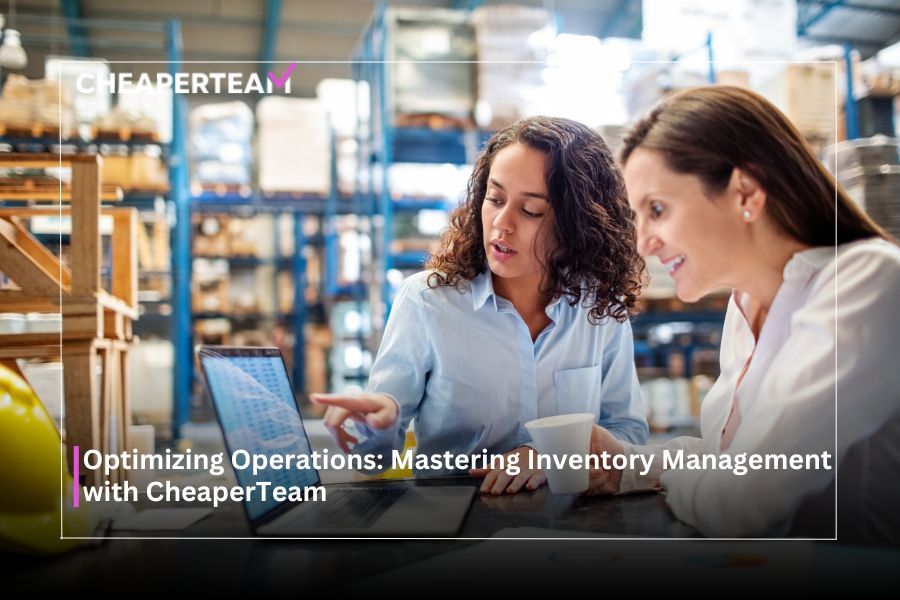
How to Calculate Service Level in Inventory Management
- Determine Demand Forecast: Estimate the demand for your product over a specific period. This can be done using historical sales data, market trends, and other relevant factors.
- Calculate Lead Time: Determine the time it takes from ordering inventory to having it available for sale. This includes supplier lead times and internal processing times.
- Calculate Safety Stock: Safety stock is the extra inventory you hold to protect against uncertainties in demand or supply. The formula for safety stock is:
Safety Stock=Z×σL\text{Safety Stock} = Z \times \sigma_LSafety Stock=Z×σL
- Z is the Z-score corresponding to your desired service level (for a 97% service level, Z is approximately 1.88).
- σL is the standard deviation of lead time demand.
- Determine Reorder Point: The reorder point is the inventory level at which you should reorder stock to avoid running out. It is calculated as:
Reorder Point=(Average Daily Demand×Lead Time)+Safety Stock\text{Reorder Point} = (\text{Average Daily Demand} \times \text{Lead Time}) + \text{Safety Stock}Reorder Point=(Average Daily Demand×Lead Time)+Safety Stock
- Set the Service Level Target: Based on the above factors, set a service level target that balances your need to meet customer demand with the costs of holding inventory.
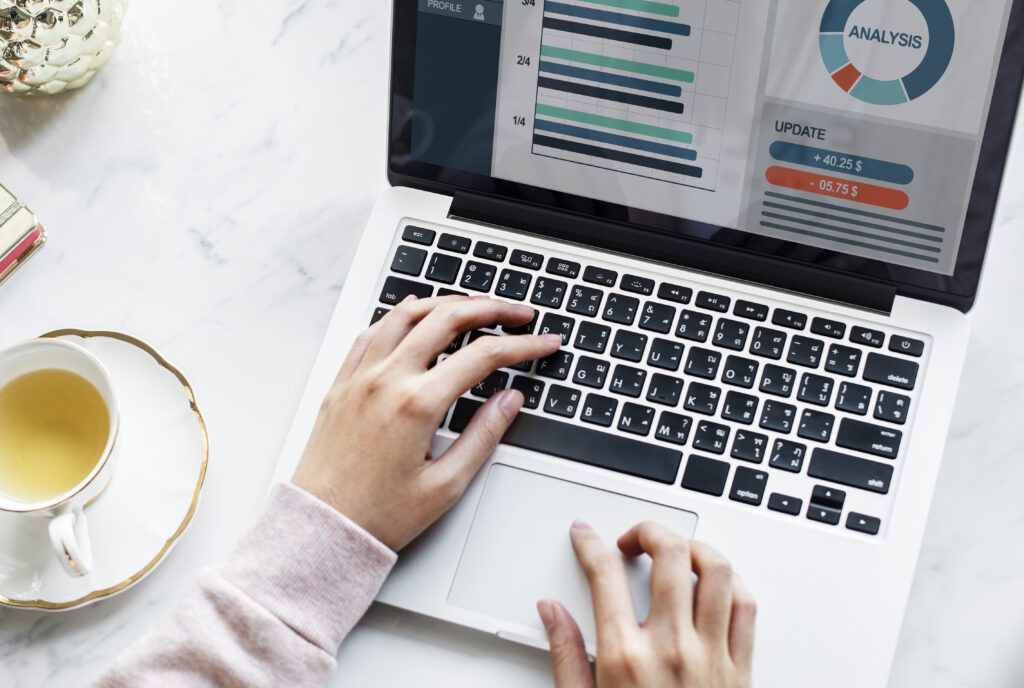
5 Ways to Set Service Level and Safety Stock Targets
- Historical Data Analysis: Use historical sales data to identify patterns and set targets based on past performance.
- Customer Expectations: Consider customer expectations and industry standards when setting service level targets.
- Cost-Benefit Analysis: Perform a cost-benefit analysis to understand the trade-offs between different service levels.
- Supply Chain Reliability: Assess the reliability of your supply chain. If your suppliers are dependable, you might be able to maintain a lower safety stock.
- Market Conditions: Adjust your service level targets based on current market conditions. For example, during peak seasons, you might aim for a higher service level.
Why Is Service Level Important in Inventory Management?
Service level is crucial because it directly impacts customer satisfaction and the efficiency of your inventory management system. A well-calculated service level ensures that you have the right amount of inventory to meet customer demand without incurring unnecessary costs.
How to Manage Inventory Control for Services
How to Calculate Service Level in Inventory Management
Inventory control for services can be more complex than for physical products, especially when dealing with intangibles like time or service availability. Here are some strategies:
- Track Service Demand: Use historical data to forecast future demand for services.
- Optimize Resource Allocation: Allocate resources based on demand forecasts to ensure that services are delivered efficiently.
- Implement Just-in-Time (JIT) Inventory: For services that rely on physical goods, implement JIT inventory practices to minimize holding costs while ensuring availability.
Why Should a Service Firm Be Concerned About Inventory Management?
Service firms should be concerned about inventory management because it impacts their ability to meet customer expectations. Poor inventory management can lead to service delays, dissatisfied customers, and lost business. Additionally, inefficient inventory management can tie up capital and increase operating costs, reducing profitability.
Conclusion: How to Calculate Service Level in Inventory Management
Calculating the service level in inventory management is a critical task that requires careful consideration of demand, lead times, and the costs associated with holding inventory and stockouts. By understanding the impact of service level on your operations and using the right tools and strategies to calculate and manage it, you can optimize your inventory management, reduce costs, and improve customer satisfaction.
Whether you are a small business or a large enterprise, setting the right service level is key to maintaining a balance between meeting customer demand and managing costs. By following the guidelines and strategies outlined in this article, you can achieve this balance and ensure the success of your inventory management efforts.